The Making of a Rifle Barrel
January 14, 2015 3:00 amGary Sandlin, the NBRSA Gulf Coast regional director, asked me recently to write an article for NBRSA NEWS describing in general terms how a rifle barrel is manufactured. I will attempt to do so without getting too technical. Hopefully I won’t reveal anyone’s “secrets”, either.
For the smaller custom barrel makers, there are two basic types of rifling methods to choose from: button rifling and cut rifling. Large manufacturers also may choose to hammer forge barrels. The capital investment required to hammer forge barrels is high, keeping it out of the reach of smaller makers. There is no loss here though, because generally speaking the quality of a buttoned or cut rifled barrel is superior to the forged types. There also has been some work being done with chemically rifled barrels, similar to an EDM process. However, I haven’t seen a barrel made by this process that looked to be of suitable quality for match shooting.
Since my experience is mostly with buttoned barrels, I’ll probably seem a little biased towards that method. Within the realm of buttoned barrels there are two methods of manufacture. The button can either be pushed or pulled through the barrel. Cut rifled barrels can be either single point cut, one groove at a time, or they might be broached. Broaching is a quicker method but requires more expensive tooling. Also the quality may be lower. Usually pistol barrels are the only type broached.
The barrel maker must choose the type of steel the barrels are made from. Most often this would be either a chrome-moly steel such as 4140 or a stainless steel such as type 416. The important characteristics of the steel are its machinability, longevity, and strength. Other considerations are secondary, such as its ability to be blued or resistance to corrosion. Almost 100% of the barrels used in competitive bench rest shooting are made from stainless steel. The grades of stainless used for barrels are fairly machinable and offer a longer accuracy life over conventional chrome-moly. They are also more resistant to some of the harsh cleaners used by accuracy shooters. A side benefit is their ability to resist corrosion.
There are several vendors of both chrome-moly and stainless steels that offer a steel suitable for manufacturing high quality rifle barrels. The steel is furnished in bar lengths of 12-20 feet and diameters suitable for the application. Most barrels for bench rest type barrels and hunting and varmint barrels are made from steel of about 1.25″ in diameter. Barrels for unlimited type rifles might be made from a larger diameter, and those for rimfire rifles from 1″ diameter or so.
The first step in making a barrel is to cut the bar to a length of 28″ or so, for a barrel that will finish to a normal length. Then the bar is placed in the drilling machine. If the material is not straight it should be trued up. Because the barrel, not the drill, spins in the machine, any imbalance in the material will cause problems. This is especially true because of the high RPM’s at which the barrel is turning.
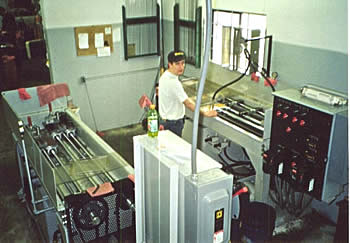
Deep hole drilling is both an art and a science. The drill does not look at all like a conventional twist drill, and many people would not recognize one for what it is. It’s a single lip drill which, if properly sharpened, is self centering. The barrel steel must also be uniform in consistency to achieve a straight hole. A small hole is in the tip of the drill and oil is pumped through the drill shank and out this hole. The oil is then forced back out of the freshly drilled hole in the barrel, and in doing so, it washes out the chips created by the drill. The oil also aids in the actual cutting.
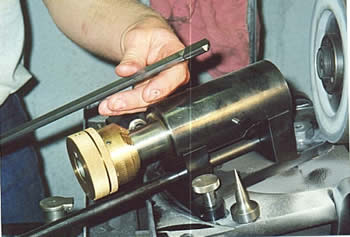
The hole diameter is intentionally drilled under the desired bore diameter for the particular caliber. After drilling, it is then brought up to size by reaming it. This process also improves the finish and uniformity of the hole. Some low quality production barrels eliminate this reaming operation as a short cut in production. Like the drill, the reamer is also flooded with cutting oil, which serves to wash away chips and facilitate the cutting action. Following reaming some makers may perform a honing operation removing a few tenths.
These first steps in making a barrel follow for either cut or buttoned barrels. Depending on the maker’s procedures, the sequence of operations may vary from this point on. With a buttoned barrel, the next step is to rifle the barrel. First the inside of the barrel is lubricated with a proprietary lube. Then the button is either pushed or pulled through the barrel. A button has a football shaped profile with grooves cut into it on a helical angle. The button is larger in diameter than the reamed hole size and is forced through the hole. The grooves in the button are the configuration of what will become the lands in the barrel. In button rifling no material is removed from the inside of the barrel. Instead the steel is moved outwards in a cold forming operation. Normally this is a one step operation, taking about a minute to actually rifle the barrel.
Although the actual rifling time is short with a button, the preparation time is more involved. A disadvantage to this method of rifling (characteristic of other cold forming operations too) is the fact that stresses are introduced into the steel. If they are not removed through heat treating, other problems may result such as potential lengthwise splitting of the barrel. Also, inside diameters may open up during the contouring stage, or warping of the barrel may occur. Fortunately these stresses can be removed through a simple heat treating operation.
Some makers will next contour the outside of the barrel, and if the barrel is to be lapped it is done after contouring. Others choose to lap the barrels prior to any outside machining. In the end, the desired result is a straight hole through a stress free piece of steel. And the inside diameter and groove depths should be uniform end to end.
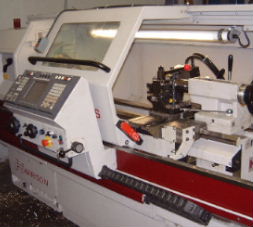
Cut barrel makers sometimes will contour a barrel before it is rifled. Since their method does not introduce any significant amount of stress to the steel it is not necessary to stress relieve the steel through heat treating. Some may choose to lap the barrels and some may not. Since the cut rifling process removes about 75% of the original surface finish left from reaming the bore, lapping may not be as important as it is with a buttoned barrel. Since some readers may not be familiar with the term lapping, I’ll describe it briefly. A lap is cast inside of the barrel and is attached to a rod similar to a cleaning rod. An abrasive is “charged” into the lap, and it is then pushed and pulled through the barrel. The object is to improve the surface finish and make the size uniform from end to end. In practice, lapping is performed by hand and is a time consuming process, requiring a good deal of experience and feel if the results are to be successful. Another advantage to lapping is that the surface finish will be parallel with the rifling. Only the best quality match grade barrels are hand lapped. No production grade barrels are.
For those who think that lapping a production barrel or a factory barrel could improve its performance, I’ll offer a little advice: don’t do it. Lapping will wear both ends of a barrel oversize. If the barrel has already been cut to length and crowned as well as chambered, this would most likely cause more harm than good. The barrel would become oversized in both the critical muzzle and throat areas. Accuracy would probably suffer.
As I mentioned, the outside contouring operation may be done at different points during manufacture. The object is to profile the barrel from its original straight cylinder condition. This is done on a lathe, and the barrel is trued between centers. This means that the outside of the barrel is true with the hole. Normally this operation is performed on a tracer lathe or a CNC type lathe. If a barrel is to be fluted, it would be done on a milling machine after turning the outside contour.
These steps are a brief outline of the various operations involved in making a rifle barrel. Not covered are the various steps and procedures in making tooling or in maintaining it. Every barrel maker has his own procedures that work best for him.
The barrel is finished now, as far as the barrel maker is concerned, and would now need to be fitted to a particular action, chambered for the desired cartridge, cut to length and crowned, and as a last step any outside finish work would be done. This outside finishing would include operations such as polishing the exterior, bead blasting, blueing, black teflon work, etc.
In a nutshell then, I have described in general terms the steps and operations involved in the manufacture of a rifle barrel. Each maker will have his own special procedures that may or may not distinguish his barrels.